What equipment is needed for the small bottle mineral water production line?
It mainly includes water treatment system, bottle blowing machine system, filling system, packaging system, etc. In the small bottle water production line, the water treatment systems of different water sources are different, but the difference is not big, only some of the equipment is different. Common water treatment equipment for small bottle water production lines includes quartz sand filters, activated carbon filters, sodium ion exchangers and precision filters. In addition to the above equipment, the bottled water production line also needs to be equipped with RO reverse osmosis. When producing mountain water and mineral water, in order to retain elements beneficial to the human body, hollow fiber filters are selected as the final filtration equipment for the water treatment system of the bottled water production line. Finally, it is pumped into a storage tank, sterilized by ozone, and introduced into a beverage filling machine for filling.
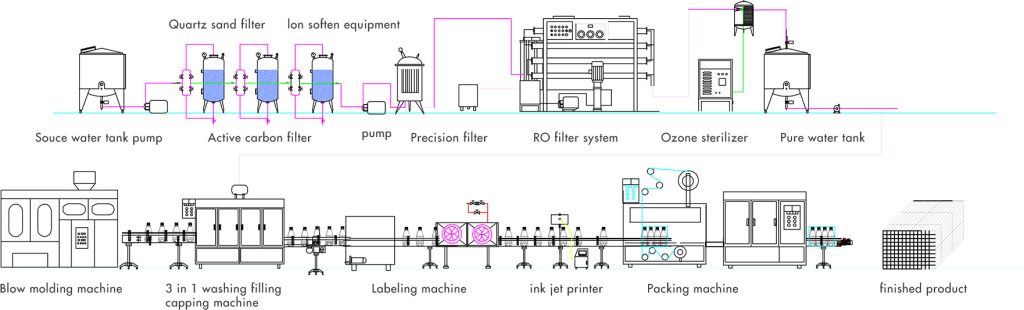
In the small bottle production line, the preforms are baked by the watering can machine at high temperature, blown into the bottle shape (bottle) by high pressure, sent to the bottle unscrambler for sorting, and then sent to the filling machine from the air duct for cleaning, filling, filling build. The beverage filling machine is the core equipment of the small bottle water production line. According to the size of the production volume, it is calculated as 500ml. The production volume below 2000 bottles/hour chooses the split type filling machine, and the production volume above 2000 bottles/hour chooses the three-in-one filling machine. installed. The semi-finished products with caps pass through the small bottle water production line sequentially through the conveyor belt (visually check whether the product has impurities), blow dry), bottle body, label), labeling machine, film packaging machine or carton packaging machine. The workshop requirements of the bottled water production line are very strict. After entering, personnel can change their clothes, wash their hands and disinfect their feet before entering the production site. The production environment of the beverage filling machine belongs to a thousand-level aseptic factory. Personnel need to change clothes twice when entering. Production can only be arranged after the reclaimed water after water treatment passes the inspection, and each bottle of finished water is sampled for inspection.